Enter T Level students – the next generation of engineers
By EngineeringUK
We know long-standing skills gaps and people shortages are a real problem for engineering businesses in England. We need more young people with the right technical skills to join the workforce. Enter T Level students – the next generation of engineers equipped with both technical expertise and practical experience. But what are T Levels, and how can T Level students benefit your business?
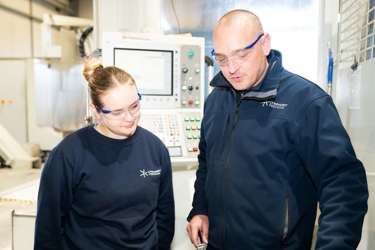
What are T Levels?
With a mix of classroom learning and an industry placement that forms 20% of the qualification, T Levels are a two-year technical course designed in partnership with the engineering and manufacturing sector to address key skills gaps. They’re a college-based technical option for students at age 16, alongside the likes of apprenticeships and A Levels.
T Levels are a high quality, rigorously tested qualification that attract high calibre students who must meet specific entry requirements and assessment criteria throughout.
Each T Level includes a 45-day industry placement where students spend time in an engineering work environment, putting their technical knowledge into action. For the business hosting these placements, they are a great opportunity to spot future employees and build a talent pipeline.
And how can T Levels help my business?
As students come armed with engineering skills from their course, they’re able to get stuck into productive work very quickly. This is what we heard from Andy Wilding, Technical manager at Lancashire-based engineering firm Lyndhurst Precision, who has hosted three T Level students on their placement so far.
‘The students come to the industry placement with industry knowledge, and ready to work. We’ve had them fabricating, we’ve had them working CNC machines and programming… we’re not making fictitious jobs for them, they’re actually helping the business.’
Many engineering businesses, such as Lyndhurst Precision, have had great success hosting T Level students for their industry placement, and many have gone on to recruit their placement students at the end of their course or offered an accelerated or higher-level apprenticeship. T Level industry placements are a proven way to find and secure new talent.
‘There’s an industry shortage of young people coming through,’ says Andy, ‘so bringing T Level students in is trying to fill that gap in the market.’
T Levels…
- Are technical qualifications for 16 to 19 year olds
- Include a 45-day industry placement that’s designed flexibly around employers’ needs
- A proven way to discover and secure high calibre new talent
How to find the right T Level student for your business
Step 1: Visit the T Levels website
Enter your postcode to find schools or colleges offering T Levels near you.
Step 2: Work with your local college or school
Consider running a short recruitment process or conducting interviews to find the right student for you. Some colleges offer ‘speed dating’ style events so businesses can meet students.
Once you’ve selected your T Level student, your local college or school can support you with planning the placement and help identify any tasks where health and safety may need addressing.
Step 3: Take on your T Level student!
Ask the school or college for details on what the students are learning and when. This will help you time the placement to fit the skills you need.
The 45-day placement can be run flexibly in blocks or day release, or even shared with another employer over 2 years.
Your school or college will support you throughout the placement answering any queries you may have.
Ready to find tomorrow’s engineering talent, today?
If you’re ready to build your future workforce by hosting a T Level industry placement, make a start now by finding your local school or college offering T Levels.
The students come to the industry placement with industry knowledge, and ready to work. We’ve had them fabricating, we’ve had them working CNC machines and programming… we’re not making fictitious jobs for them, they’re actually helping the business.
— Andy Wilding, Technical Manager, Lyndhurst Precision